How to Optimise Small Jaw Crusher Parts Performance and Production Capacity?
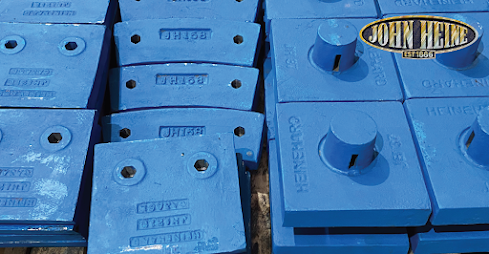
When it comes to gaining higher economic profit, it is vital to get the most out of the crushing equipment, and jaw crusher parts are no exception. The performance and production capacity of a jaw crusher impact the business ROI of investors. The production capacity of the jaw crusher gets affected by several factors, usually due to the material's physical properties such as hardness, size and bulk density. Here are some crucial solutions to optimise or improve jaw crusher production capacity. Consider the Proper Jaw Profile The crushing equipment like jaw crushers has the primary role of crushing different size rocks. The efficiency of crusher parts varies based on rocks' crushability, abrasiveness, and flakiness. However, choosing the best adjustment of fixed and movable jaw dies profiles will help improve the production capacity while crushing tough material. Opting for a proper Jaw profile can save at least 20% of production efficiency, which would otherwi